Uno de los principales focos de pérdida en los procesos de fabricación son las paradas de máquina por cambio de utillajes, tareas de limpieza o mantenimiento. Aunque se trate de paradas planificadas, si el tiempo de cambio es elevado, genera otros desperdicios asociados, como la necesidad de producir en grandes lotes y, en consecuencia, el aumento del stock.
La buena noticia es que esta pérdida se puede reducir de forma significativa aplicando la metodología adecuada. Nuestra experiencia demuestra que los resultados son visibles desde el primer taller, con un retorno muy alto y mejoras sostenidas en el tiempo.
RESULTADOS HABITUALES
70% -50% de reducción del tiempo de parada.
12% Mayor disponibilidad máquinas.
Mayor capacidad para producir en lotes más pequeños.
Mayor flexibilidad y capacidad de respuesta a la demanda del cliente.
Autonomía del equipo de producción para realizar el cambio/ menor dependencia de mantenimiento.
Disminución de los costes por la bajada tiempo de parada.
¿Qué herramienta usamos?
Los responsables de proyectos de mejora disponemos de una herramienta Lean específica para optimizar los cambios de formato: SMED (Single Minute Exchange of Die). Esta metodología permite reducir los tiempos de cambio de forma estructurada y sostenible.
Entender el tiempo de cambio
Existen diferentes visiones. La más extendida es la que define el tiempo de cambio como:
«El periodo desde la salida del último producto válido de la referencia previa, manufacturado a la velocidad nominal, hasta la salida del primer producto válido de la siguiente serie producido a la velocidad nominal.»
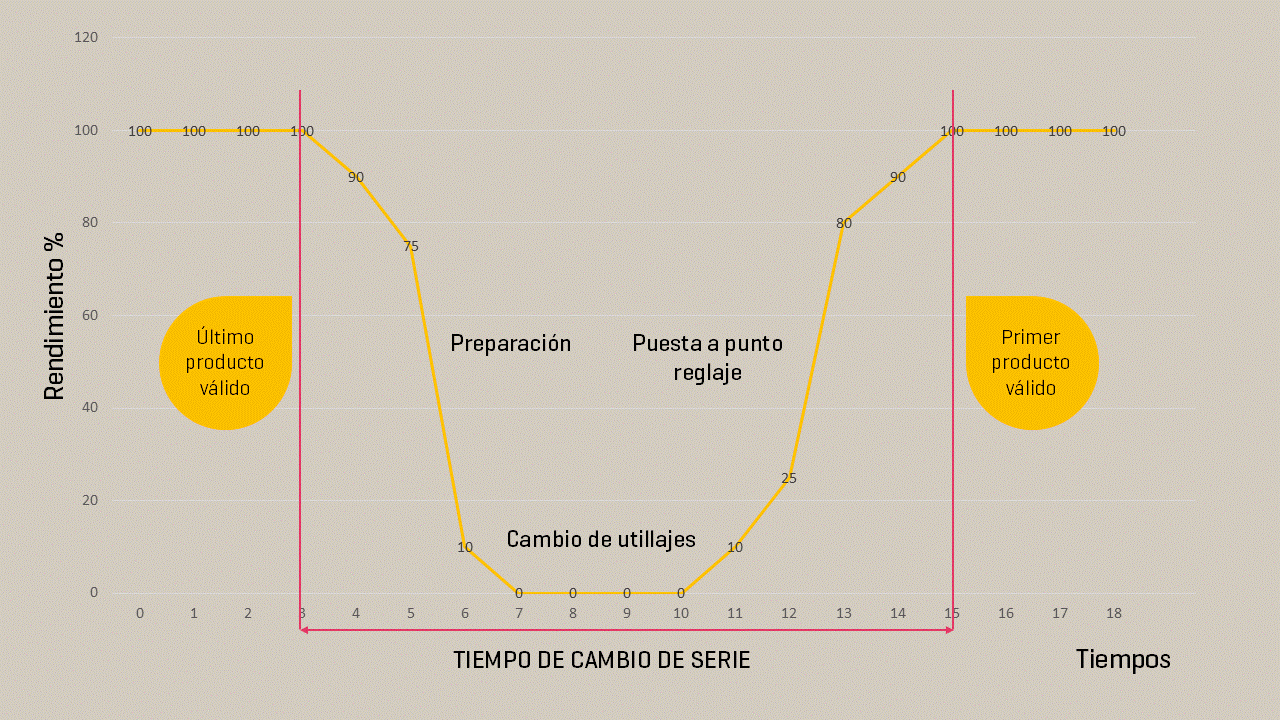
¿Cómo reducimos los tiempos de cambio?
La metodología SMED se implementa habitualmente en talleres Kaizen, combinada con otras herramientas Lean como las 5S, la gestión visual y la estandarización. Consta de seis etapas:
1. Medición del tiempo total de cambio.
El primer paso es registrar el proceso real mediante vídeo. Esta grabación se analiza en sala para desglosar todas las tareas, tiempos, incidencias y movimientos implicados, y así establecer una línea base.
2. Clasificación de tareas: internas vs. externas
Se identifican qué tareas requieren la máquina parada (internas) y cuáles pueden hacerse con la máquina en marcha (externas).
- Tareas internas: manipulación directa de la máquina (por ejemplo, desmontaje de piezas).
- Tareas externas: actividades como la preparación de utillajes o trámites administrativos.
Antes de avanzar, se aplican las 5S en el puesto para facilitar que el mayor número posible de tareas se conviertan en externas y se anticipen.
En la imagen, un ejemplo de hoja de toma de tiempos. En verde, la operaciones internas, y en rojo las externas.
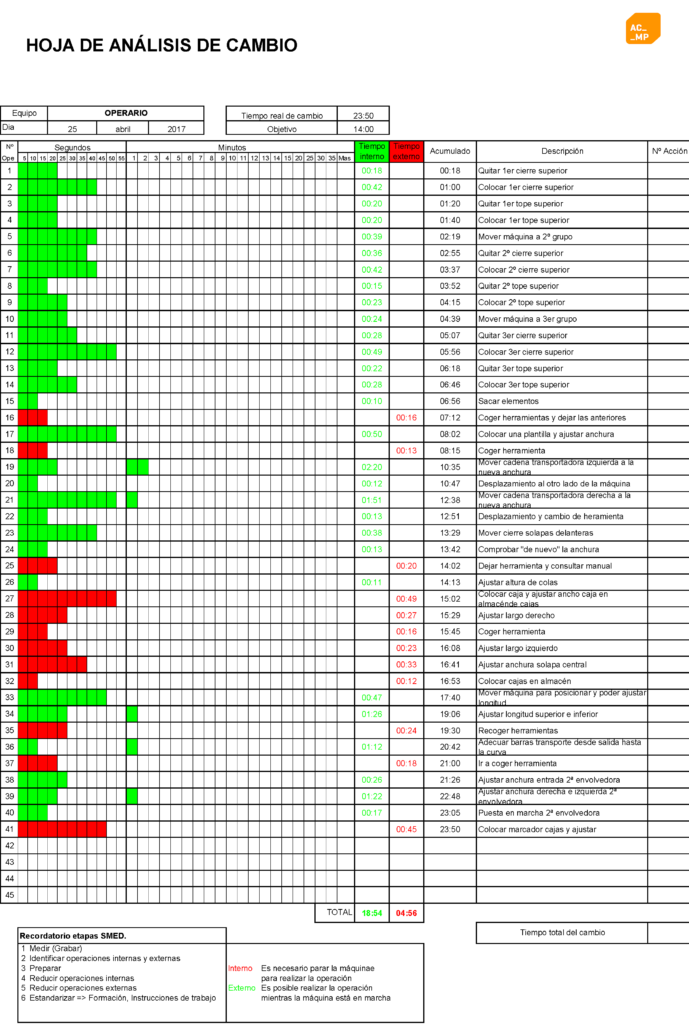
3. Transformar las tareas internas en tareas externas.
El objetivo es maximizar las actividades que pueden hacerse con la máquina en funcionamiento. Algunas acciones frecuentes son: calentar moldes previamente, duplicar utillajes, usar piezas premontadas, etc. Todas estas mejoras se recogen en un plan de acción con responsables y plazos definidos.
4. Reducir las tareas internas.
Las tareas que no se pueden externalizar se deben simplificar. Esto incluye acciones tipo:
- Sustituir tornillos por palomillas u otros sistemas rápidos.
- Estandarizar ajustes con calces o topes.
- Añadir marcas visibles para facilitar el posicionamiento.
- Ejecutar operaciones en paralelo.
5. Reducir las tareas externas.
Algunas referencias unen los pasos 4 y 5 en una única etapa. Aquí los mostramos de forma separada para subrayar la importancia de reducir todas las actividades, sean internas o externas. Aunque a menudo se pasa por alto, las tareas externas pueden representar entre el 30 % y el 50 % del tiempo total de cambio. Esta etapa busca optimizarlas tanto como las internas.
6. Estandarizar el nuevo procedimiento de cambio.
Una vez rediseñado el proceso de cambio, se documenta mediante instrucciones de trabajo consensuadas con el equipo operativo. ¿Cómo se controla la efectividad del nuevo estándar? El seguimiento se integra en las auditorías de 5S y en las reuniones de revisión de indicadores, donde se analizan tiempos, desviaciones y acciones correctivas.
¿Cuánto tiempo se tarda en ver resultados?
El plazo varía según el tipo de cambio, su complejidad, el número de personas implicadas o el grado de madurez del sistema de gestión. Aun así, el esquema general es:
- Preparación (≈1 mes)
Se identifican oportunidades, se conforma el equipo y se planifican las acciones de formación y sensibilización.
- Despliegue e implementación (1 a 3 meses)
Se aplican las seis fases SMED, se validan mejoras y se monitorizan resultados.
En muchos casos, las mejoras son tangibles desde el primer taller Kaizen. Aquí puedes consultar un caso práctico real.
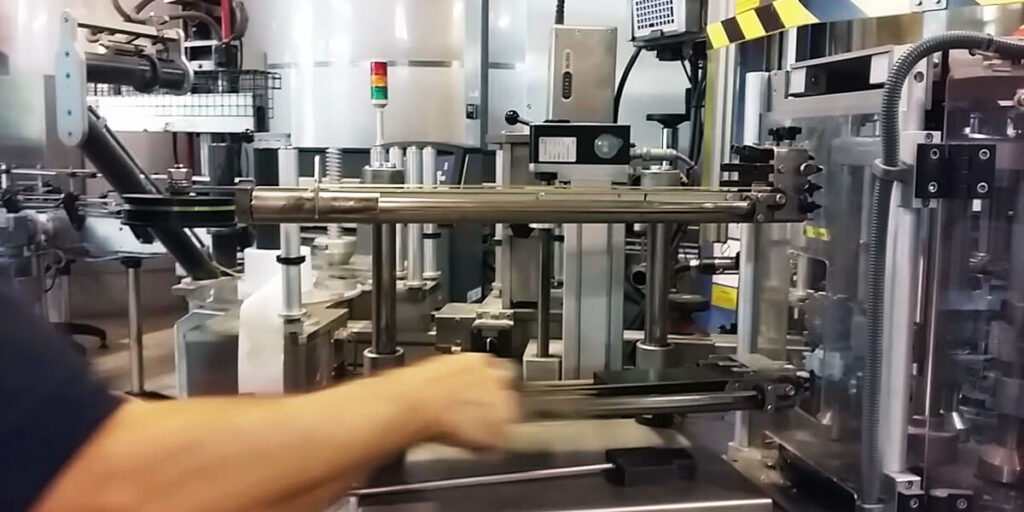
Recomendaciones del equipo ACMP para una implementación eficaz
- Sensibiliza al equipo: una plantilla comprometida facilita el cambio.
- Forma al personal en los principios de SMED y en los nuevos procedimientos.
- Destina los recursos necesarios: tiempo, herramientas, formación, etc.
- Involucra a múltiples áreas: producción, mantenimiento, logística, ingeniería…
- Avanza con objetivos realistas, sobre todo en los primeros ciclos.
- Sigue el orden de las etapas y registra los avances en cada una.
- Repite el ciclo: siempre es posible mejorar más.
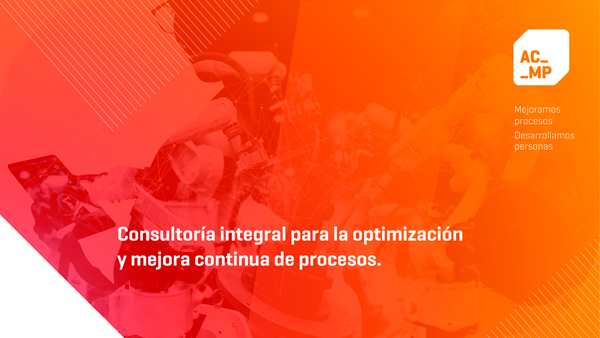
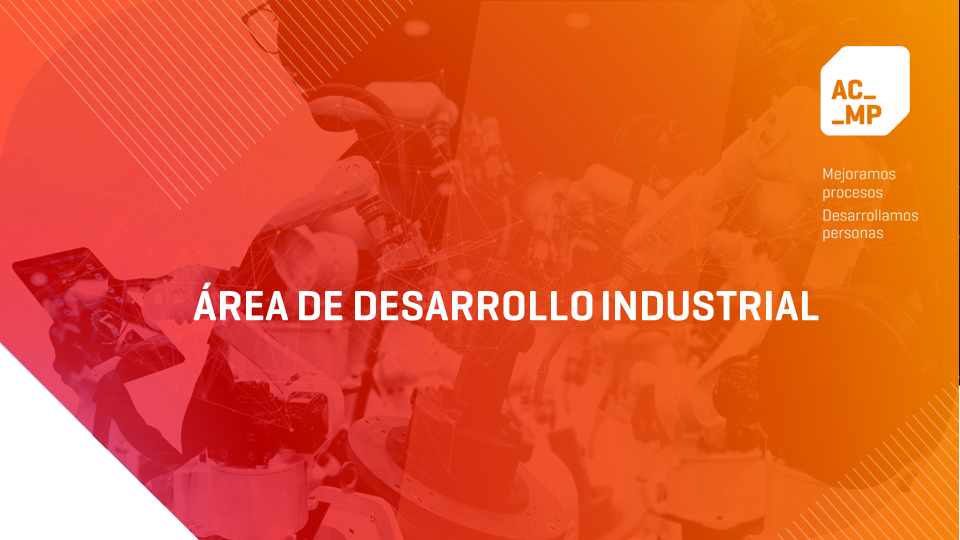
Desarrollo industrial y escalado de pymes
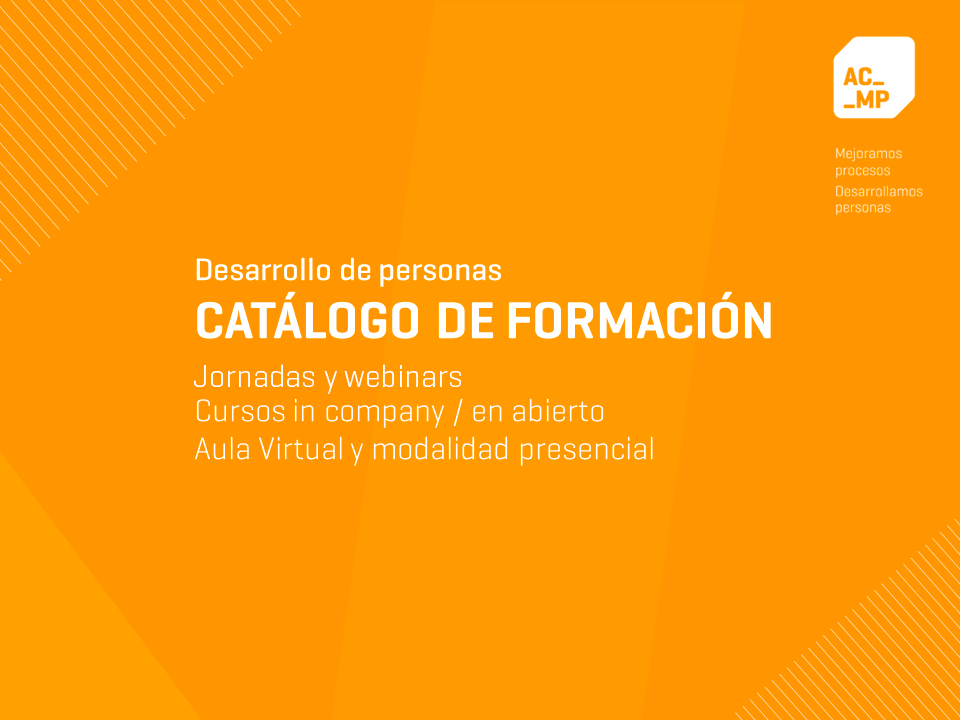
Últimas noticias
- ebook gratuito crecer sin colapsar
- ¿Reuniones improductivas? cómo convertirlas en una herramienta imprescindible para mejorar tu operativa
- ¿Tu pyme crece pero tu equipo está desbordado? Necesitas una organización sólida y elástica para dar el salto con garantías
- Optimización Avanzada de Procesos: Más Eficiencia, Menos Costes
- Nueva convocatoria de ayudas para mejorar la competitividad de tu empresa en Navarra
¡Síguenos!
Te acompañamos en todo el proceso, desde el análisis inicial hasta la implementación de mejoras.
Contáctanos y descubre cómo empezar a ganar eficiencia desde el primer día.