Los eventos kaizen son una poderosa herramienta de mejora continua al alcance de cualquier empresa. Un kaizen sirve para analizar en profundidad un proceso, identificar sus despilfarros, las causas raíz de esas improductividades y crear un nuevo proceso más eficiente.
Como ya apuntábamos en el post anterior, su intensidad e inmediatez los convierte en instrumentos altamente eficaces que generan resultados en muy poco tiempo.
Pero también son una buena oportunidad para el aprendizaje a todos los niveles. El equipo aprende de forma práctica y sistemática a implementar las herramientas de mejora, a analizar situaciones problemáticas y plantear ideas que las resuelvan de manera duradera. Para los responsables, supone incrementar sus habilidades como gestores de la mejora continua, y en consecuencia, ganar autonomía en este campo.
Objetivo kaizen: impulsar la eficiencia, la satisfacción del cliente y reducir costes
Un evento kaizen es, ante todo, una metodología participativa con la que se involucra a las personas que trabajan directamente en el proceso. La gente tiene que cuestionar sus propias dinámicas de trabajo, aplicar su experiencia y discurrir nuevas formas para mejorarlo. Contribuye, por tanto, a potenciar el sentimiento de propiedad sobre el proceso.
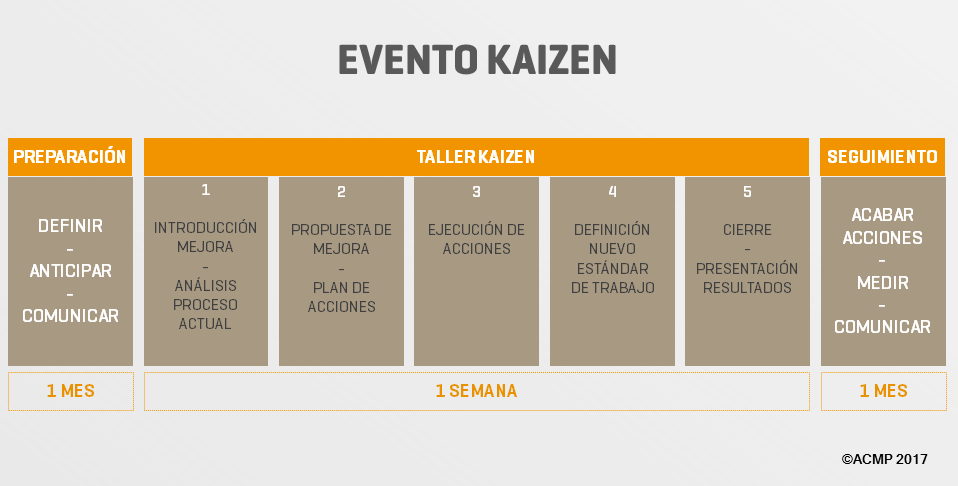
¿Cómo se desarrolla un taller kaizen en la práctica? Por lo general, el taller se desarrolla en cinco etapas:
1.El primer día de taller arranca con la puesta en común con el equipo de los objetivos y las pautas de trabajo del taller, seguido de un repaso de los conceptos lean. Los participantes realizan entonces una primera reflexión sobre las causas del problema seleccionado y las posibles soluciones a fin de obtener una visión global y conjunta. Se presenta la herramienta que se va a usar según el objetivo del taller (5S, SMED, Kanban…) y se procede al análisis del proceso actual, usando para ello la herramienta más adecuada.
2. Elaboración de un plan de acciones que recoja todas las ideas de mejora propuestas por el equipo, asignarles una prioridad para su puesta en marcha, bien durante o tras el taller, y al responsable de ejecutarlas.
3. Se realizan las acciones de mejora sobre el proceso, en planta u oficina. En este punto, de lo que se trata es de probar y medir el impacto de las actuaciones, aunque no sean la solución definitiva.
4. Definición del nuevo estándar de trabajo del proceso mejorado, por una parte los estándares relativos a seguridad, calidad, flujo de materiales etc. y, por otro, las instrucciones de cada puesto, siempre visibles y visuales.
5. Presentación a dirección de las acciones que se han realizado, los resultados logrados por el equipo y el plan de acciones que han quedado pendientes y que se suelen implementar a lo largo de las cinco semanas siguientes.
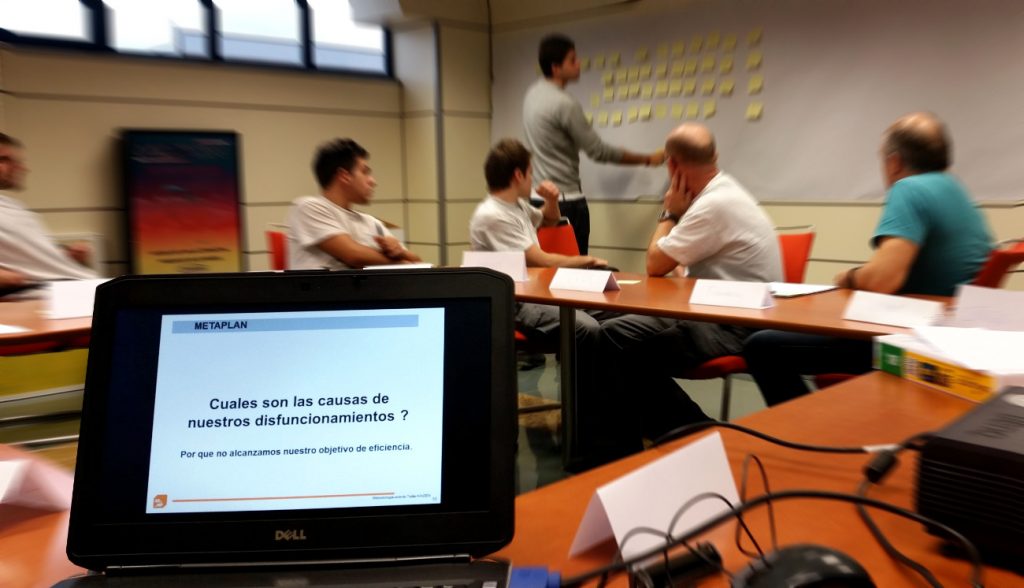
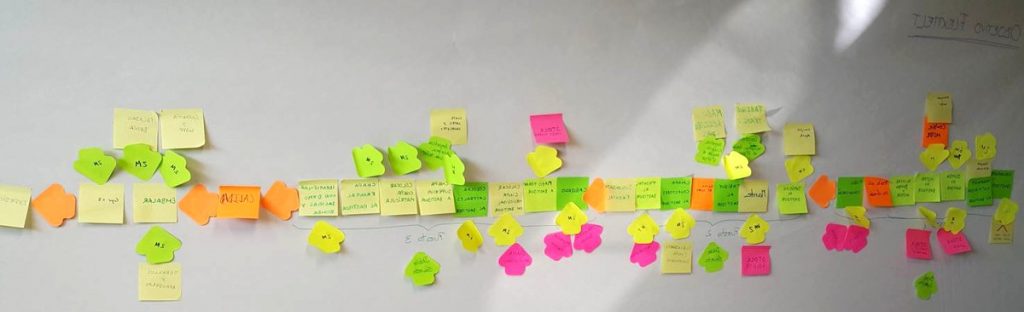
Lecciones aprendidas y recomendaciones del equipo de ACMP
- El compromiso de la dirección con la actividad es clave para garantizar su éxito, como lo es la participación del responsable del área sobre la que se actúa.
- Una preparación previa bien realizada contribuye a sacar el mayor provecho del taller.
- La comunicación durante todas las fases de la actividad es vital. Hay que trasladar los objetivos del proyecto, su alcance, las acciones y resultados.
- El líder del taller debe asegurar el cumplimiento de la metodología y las pautas de trabajo del taller: orientar al equipo, controlar los tiempos, etc.
- La capacidad para detectar el despilfarro y las oportunidades de mejora se desarrolla poco a poco. De ahí que la contribución del facilitador sea esencial y una oportunidad para transferir esas habilidades al equipo.
CASO PRÁCTICO I
En una compañía fabricante de equipos de aplicación de adhesivo se organiza un taller de mejora de una semana para optimizar el proceso de montaje de una de sus líneas. Se elabora un plan de acción de más de 50 acciones, 12 de las cuales se implementan en el evento: nuevo lay out, puestos de trabajo y sistema de aprovisionamiento, entre otros. Se logra reducir un 62% el tiempo del proceso y un 30% la superficie empleada.
CASO PRÁCTICO II
Una empresa del sector agroalimentario necesita reducir el tiempo de cambio de formato de los equipos, concretamente los de la única de línea de embotellado de la planta por la que pasan diferentes referencias de producto. Se organiza un taller kaizen de dos días para implantar el método SMED en el que participan ocho personas. El resultado: disminución del tiempo de cambio en un 70%.
Ver más casos prácticos
Posts relacionados: