La Planificación Avanzada de la Calidad del Producto (APQP en sus siglas en inglés) es una metodología estructurada diseñada para garantizar que los productos cumplan con los requisitos de calidad y desempeño desde las primeras etapas de desarrollo.
Esta metodología, que surgió en la industria automotriz de EEUU en los años 80, se ha expandido a sectores como el aeroespacial, renovable o el farmacéutico. APQP no sólo asegura que los productos lleguen al mercado a tiempo y con los estándares de calidad requeridos, sino que también facilita la comunicación efectiva entre todas las partes involucradas, desde los proveedores hasta los clientes.
Con más de 4.000 empresas asociadas a nivel global, la AIAG es la organización que mantiene la norma APQP. El pasado mes de marzo publicó la 3ª edición del Manual APQP junto con la 1ª edición independiente del Plan de Control.
¿QUÉ ES LA METODOLOGÍA APQP?
El APQP es un enfoque sistemático para gestionar el ciclo de vida del producto, desde la planificación inicial hasta el seguimiento tras el lanzamiento. Su objetivo es garantizar que los productos satisfagan las expectativas del cliente, cumpliendo con estrictos estándares de calidad. Esto se logra mediante la participación de un equipo multidisciplinar y la implementación de un proceso riguroso para prevenir posibles fallos y desviaciones en las fases de diseño y producción.
La metodología APQP está centrada en facilitar la colaboración entre los diferentes equipos, asegurando que cada paso del proceso esté alineado con las expectativas del cliente y los requisitos técnicos.
La mayoría de fabricantes del sector automoción (OEM) o energías renovables (APQP4Wind) exigen como requisito a sus proveedores la aplicación del APQP.
BENEFICIOS DEL APQP
La implementación del APQP ofrece varios beneficios que mejoran tanto la eficiencia de los proyectos como la calidad final del producto:
1. Asegura el «time to market»
Facilita el cumplimiento de los plazos de lanzamiento con un enfoque en la eficiencia y la reducción de costos, lo que ayuda a los responsables a priorizar tareas y asignar adecuadamente activos y suministros.
2. Focaliza los recursos en las necesidades del cliente.
Al comprender desde el inicio los requisitos del cliente, se optimizan los esfuerzos y se minimizan las sorpresas.
3. Previene fallos desde la fase inicial.
El APQP permite identificar y resolver potenciales problemas antes de que afecten la producción.
4. Colaboración entre departamentos.
Fomenta el trabajo conjunto y una comunicación fluida de todos los equipos involucrados, desde ingeniería hasta producción, lo que mejora la eficacia operativa.
5. Mejora de la calidad
Gracias a su enfoque metódico, la metodología permite que el producto cumpla con los más altos estándares de calidad desde el principio. Además, fomenta una mentalidad Cero Defectos en la organización.
6. Gestión de riesgos proactiva
El marco APQP identifica posibles riesgos desde la planificación y permite abordarlos con acciones preventivas y correctivas.
¿Necesitas implementar en tu empresa la metodología APQP?
Nosotros te acompañamos durante todo el proceso con ayuda experta, para que logres tus objetivos en el menor tiempo posible.
CÓMO IMPLEMENTAMOS EL APQP
El APQP se desarrolla en cinco fases principales, cada una con un conjunto de tareas específicas que aseguran la correcta planificación y ejecución del proyecto.
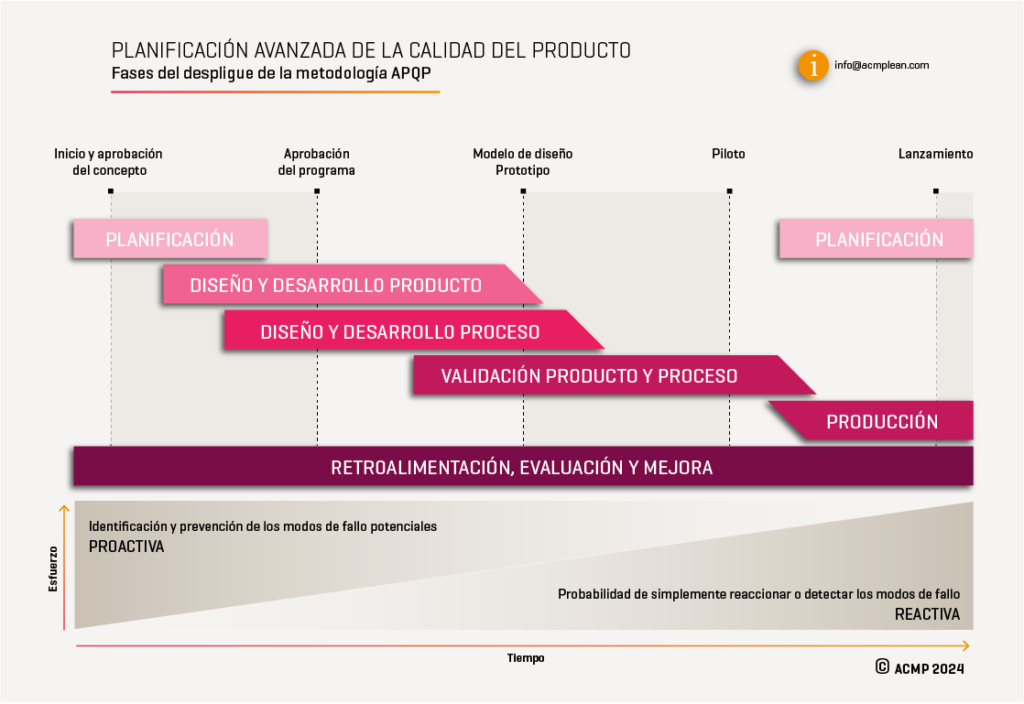
1. CREACIÓN DEL EQUIPO
Se forma un equipo de trabajo multidisciplinar que incluye a personal de ingeniería, calidad, producción y otros departamentos clave. Este enfoque asegura que todas las perspectivas y requisitos técnicos se consideren desde el principio del proyecto.
➜ Consideramos esencial formar y sensibilizar al personal sobre las herramientas que se van a utilizar a lo largo del proceso: APQP, AMFE, MSA, SPC, PPAP, entre otras.
➜ Establecer roles y responsabilidades claras es esencial para evitar posibles fallos de comunicación en el trabajo en equipo.
➜ Asignar recursos de forma que se asegure la disponibilidad de las personas para el trabajo en el nuevo proyecto APQP.
2. PLANIFICACIÓN Y DEFINICIÓN DEL PROGRAMA
En esta fase, se identifican los requisitos del cliente y se traduce su voz en términos técnicos y operativos. Para ello, se utilizan diferentes inputs como la VOC, análisis de mercado, confiabilidad del producto, plan de negocio y marketing y otros factores clave.
También se identifican los objetivos del proyecto, los plazos, las responsabilidades de cada equipo y los recursos necesarios. El resultado es un plan claro y detallado que guiará las siguientes etapas. Este plan debe abordar los requisitos de calidad, costo, tiempos de entrega y otras especificaciones críticas para garantizar que el desarrollo del producto cumpla con los estándares acordados.
➜ Es fundamental comprender a fondo las expectativas del cliente, ya que de esto depende el éxito del proyecto.
3. DISEÑO Y DESARROLLO DEL PRODUCTO
Se crea el diseño conceptual del producto, en el que se establecen las características clave y los criterios de aceptación. Algunas de las actividades críticas de esta fase incluyen:
- Fabricación de un prototipo y pruebas para verificar su conformidad con los objetivos de calidad y desempeño según la VOC.
- Evaluación de la viabilidad técnica y económica del diseño.
- Análisis de los posibles problemas que puedan surgir en la producción.
Esta fase garantiza que el producto, antes de pasar a la etapa de producción, sea viable y cumpla con las exigencias de los clientes y del mercado.
➜ Involucrar a todos los departamentos relevantes para asegurar la viabilidad del diseño tanto desde el punto de vista técnico como económico.
4. DISEÑO Y DESARROLLO DEL PROCESO
En esta fase se diseñan y establecen los procesos de fabricación que serán utilizados para producir el producto. Se determinan las máquinas, herramientas, técnicas y métodos de producción necesarios para cumplir con los volúmenes de producción requeridos y las especificaciones de calidad. Además, se optimizan los procesos para garantizar que sean eficientes y efectivos.
Aquí también se crean unos Planes de control detallados, que son documentos esenciales que describen cómo se controlarán los procesos, cómo se medirán los resultados y qué acciones correctivas se tomarán si se detectan desviaciones. Son esenciales para garantizar que los procesos de producción se mantengan dentro de los parámetros establecidos.
- Pruebas piloto para validar que los métodos de producción son efectivos.
- Optimización de los flujos de trabajo y la utilización de recursos.
- Identificación de los controles críticos para asegurar la calidad del producto.
➜ Las tareas a realizar en esta fase del proceso APQP dependen de haber completado adecuadamente las dos fases anteriores.
➜ Solapar las tareas para ser más eficientes, ganar fechas e integrar las diferentes funciones de la empresa.
➜ Estandarizar productos, procesos, tecnologías, componentes, métodos, etc. con el objetivo de mejorar la calidad y eficiencia del proceso.
5. VALIDACIÓN DEL PRODUCTO Y DEL PROCESO
Se realizan pruebas para confirmar que tanto el producto como el proceso cumplen con los estándares de calidad y las especificaciones del cliente. Es fundamental llevar a cabo una serie de producción piloto significativa para verificar que todo funcione como se planificó.
Durante esta etapa, se revisan y ajustan los planes de control y los diagramas de flujo del proceso de fabricación para asegurar que se sigan correctamente y se detecte y corrija cualquier problema antes de la producción a gran escala.
Los resultados del APQP forman la base para el proceso de aprobación de piezas recogido en el PPAP.
6. RETROALIMENTACIÓN, EVALUACIÓN Y MEJORA
Tras el lanzamiento al mercado, se sigue de cerca la aceptación del producto por parte de los clientes, recogiendo información para identificar futuras mejoras y asegurando la calidad continua en la producción a largo plazo.
El equipo de producción y calidad revisa los datos obtenidos de las pruebas de control de calidad y ajusta los procesos cuando es necesario para asegurar que se mantengan los estándares de producción y satisfacción del cliente.
➜ El Plan de Control y las auditorías periódicas desempeñan un papel crucial, asegurando que el proceso mantenga su nivel de calidad y eficiencia en el tiempo.
➜ La Planificación de la Calidad también efectuarse siempre que se implemente un cambio de producto o proceso tras el lanzamiento y la validación del proceso, incluyendo el PPAP para el cambio implementado.
Con todo lo dicho, podemos concluir que el APQP es un herramienta es clave para las empresas que buscan garantizar la calidad de sus nuevos productos, minimizando tiempos de entrega e imprevistos.
Su enfoque en la planificación temprana, la colaboración entre departamentos y la gestión de riesgos proactiva permite una mejor alineación con las expectativas del cliente y reduce los posibles fallos durante la producción.
Aunque su implementación puede presentar ciertos retos, los beneficios en términos de eficiencia, reducción de costos y mejora continua la convierten en una metodología indispensable para sectores industriales altamente regulados como la automoción, renovables y farmacéutico.
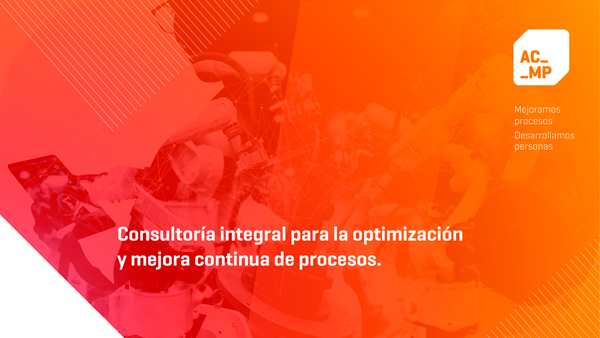
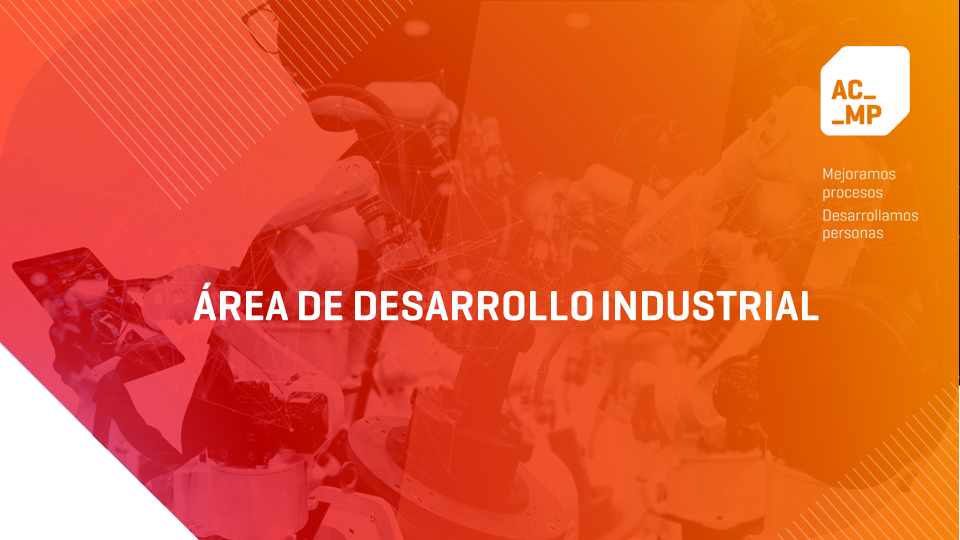
Desarrollo industrial y escalado de pymes
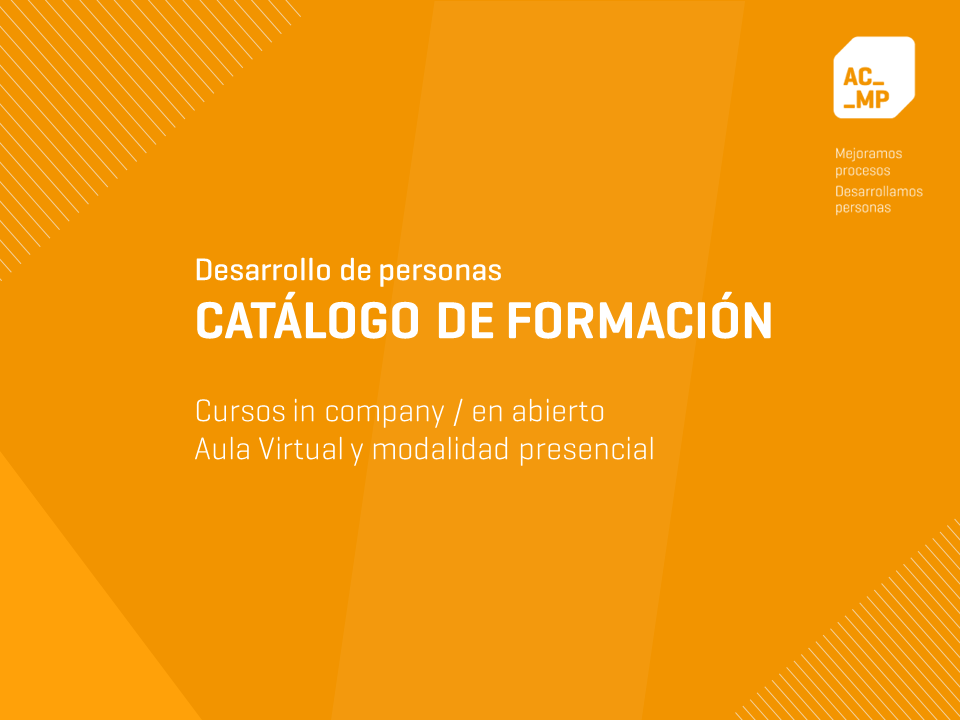
Últimas noticias
- ebook gratuito crecer sin colapsar
- ¿Reuniones improductivas? cómo convertirlas en una herramienta imprescindible para mejorar tu operativa
- ¿Tu pyme crece pero tu equipo está desbordado? Necesitas una organización sólida y elástica para dar el salto con garantías
- Optimización Avanzada de Procesos: Más Eficiencia, Menos Costes
- Nueva convocatoria de ayudas para mejorar la competitividad de tu empresa en Navarra