Crédito imagen portada: ©alotofpeople - stock.adobe.com
Una de las principales pérdidas que se generan en producción es la parada de las máquinas debido al cambio de utillajes, las tareas de limpieza o por mantenimiento.
Cuando el tiempo de cambio es largo provoca, a su vez, la aparición de otros desperdicios, como un aumento del stock por la fabricación en grandes lotes.
SMED (del inglés Single Minute Exchange of Die) es una técnica de mejora Lean esencial cuya aplicación permite a la empresa disminuir los tiempos de cambio y comporta numerosos beneficios, como:
- La reducción de los despilfarros: sobreproducción, inventario, espacio ocupado, transportes o movimientos de los operarios
- Un aumento de la capacidad para fabricar un mayor número de referencias en menos tiempo
- Mayor flexibilidad de las líneas de producción para responder a las variaciones de la demanda del cliente y rapidez de entrega
- Una disminución de los costes de producción
¿QUÉ ES EL TIEMPO DE CAMBIO?
Existen diferentes visiones. La más extendida lo define como el periodo desde la salida del último producto válido de la referencia previa, manufacturado a la velocidad nominal, hasta la salida del primer producto válido de la siguiente serie producido a la velocidad nominal.
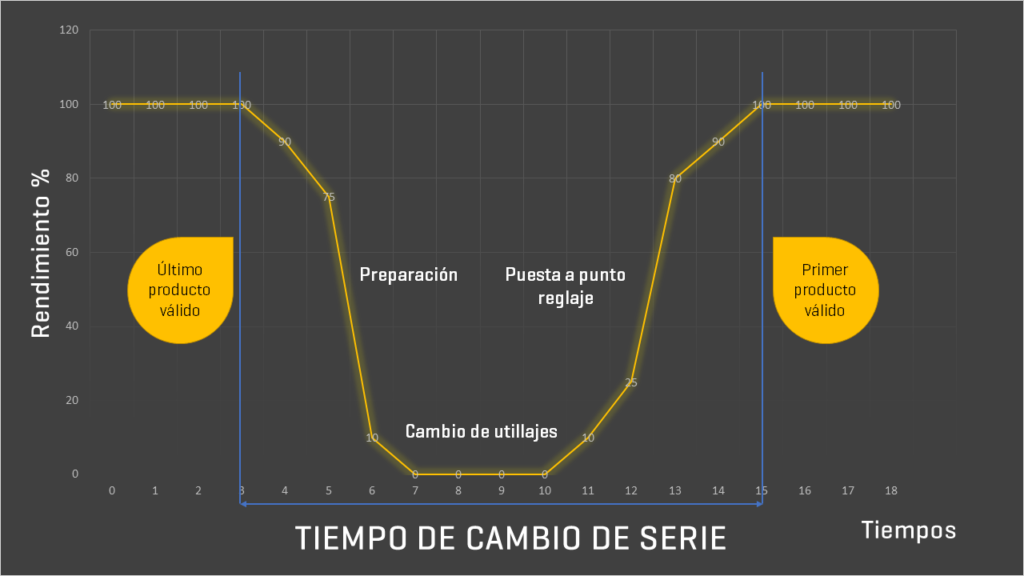
¿CÓMO SE REALIZA UN SMED?
La metodología SMED consta de seis pasos y se implementa en combinación con otras herramientas Lean, como las 5S, la gestión visual, el taller kaizen y la estandarización.
1. Medición del tiempo total de cambio.
El objetivo en esta fase es obtener información real sobre el proceso de cambio de formato que posteriormente analizará el equipo. Para ello, se graba un vídeo in situ que registre todas las operaciones y movimientos efectuados por el personal durante el cambio. Ya en sala, se pormenorizan los datos (desglose de tiempos, tareas, incidencias, movimientos, etc.) y se determina el tiempo de cambio actual a partir del visionado de la grabación.
2. Se identifican y clasifican las actividades internas y externas.
En este punto se trata de diferenciar las tareas internas, aquellas operaciones que deben hacerse obligatoriamente con la máquina parada, de las externas, las que se pueden realizar con la máquina en marcha normal.
Todas las tareas que impliquen tocar la máquina, por ejemplo, desmontar una pieza o cambiar un tornillo, son internas. Por su parte, la preparación de los utillajes del cambio o un trámite informático, se denominan tareas externas.
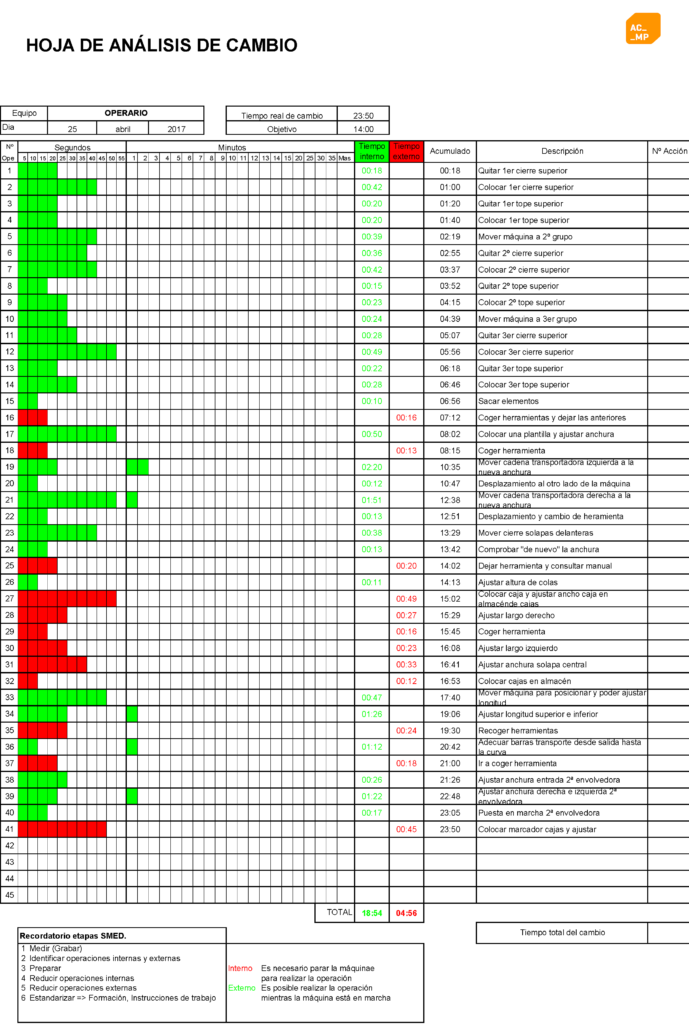
Ejemplo de hoja de toma de tiempos. En verde, la operaciones internas, y en rojo las externas.
Antes del siguiente paso, es imprescindible implementar las 5S en el puesto donde se realiza el cambio para eliminar operaciones externas. Puesto que éstas se realizan con la máquina en funcionamiento, se pueden anticipar tareas: reorganizar el espacio de trabajo, seleccionar y preparar las piezas necesarias, comprobar el material del puesto, limpiar utillajes, etc.
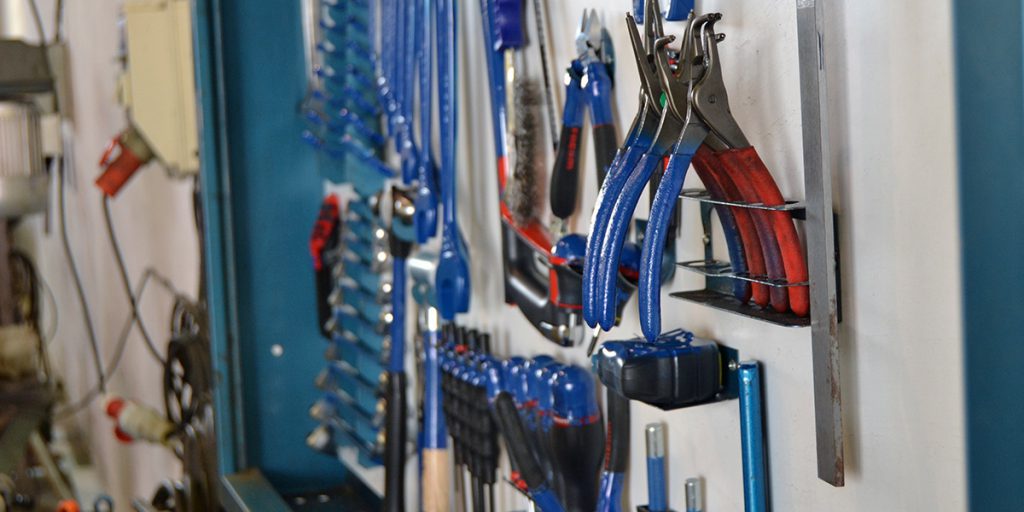
3. Transformar las tareas internas en tareas externas.
En esta etapa se implementan las mejoras detectadas, encaminadas a maximizar las actividades externas y reducir las internas. A modo de ejemplo, calentar con antelación el molde, duplicar los utillajes que se usan, incorporar piezas premontadas, etc.
El plan de acción especifica actividades, plazos y responsables.
4. Reducir las tareas internas.
El objetivo es actuar sobre las restantes tareas internas para acortar el tiempo que ocupan. Existen muchos trucos, desde eliminar los tornillos y sustituirlos por mecanismos de apertura, como palomillas, u otro tipo de sujeciones funcionales; transformar los ajustes en sistemas de fijación múltiple; usar marcas visibles; usar calces para estandarizar el ajuste de la medida, crear operaciones paralelas, etc.
5. Reducir las tareas externas.
Algunas referencias bibliográficas unen los pasos 4 y 5 en una única etapa. Aquí los mostramos de forma separada para subrayar la importancia de reducir todas las actividades, sean internas o externas. Con frecuencia los equipos de mejora centran sus esfuerzos en minimizar las operaciones internas y no prestan atención a las externas, que suponen entre el 30% y el 50% del tiempo de cambio.
En esta fase, la misión del equipo es plantear e implementar mejoras que minoren el tiempo empleado en las actividades externas.
6. Estandarizar el nuevo procedimiento de cambio.
El nuevo estándar se formaliza mediante instrucciones de trabajo, que es conveniente elaborar con la participación y el visto bueno de las personas que habitualmente realizan el cambio de formato.
¿Cómo se controla la efectividad del nuevo estándar? Incluyéndolo en las auditorías de 5S y en las reuniones diarias de revisión de indicadores operativos, donde se hace el seguimiento de los registros de tiempos de cambio, las posibles desviaciones y se determinan acciones correctoras.
¿CUÁNTO DURA UN PROYECTO SMED?
La implementación varía de un proyecto a otro en función del tipo de cambio que se aborde, su complejidad, el número de personas involucradas, si la empresa cuenta con un sistema de gestión y seguimiento de indicadores o hay que incorporarlo, entre otras variables.
Existe una fase previa de preparación, que suele desarrollarse en un mes, durante la que se identifican y priorizan oportunidades, se crea el equipo de proyecto y se llevan a cabo las acciones de comunicación, sensibilización y formación que se hayan previsto.
A partir de aquí se despliegan las seis fases descritas y una vez concluidas, y por lo que respecta a ACMP, se hace el seguimiento de las mejoras para comprobar que su desarrollo y mantenimiento es correcto. Este trabajo suele durar entre uno y tres meses.
Los resultados normalmente son rápidos y visibles a partir del primer taller kaizen. Aquí podéis consultar un caso real.
CLAVES PARA ASEGURAR EL ÉXITO
- Sensibiliza al equipo: de esta manera se favorece la receptividad al cambio y la percepción de los beneficios del SMED: mayor flexibilidad, eficiencia, servicio al cliente.
- En la misma línea, es esencial formar del personal en los principios y pautas de la metodología de trabajo para que lo apliquen.
- Destina recursos para llevar a cabo las mejoras: herramientas, formación, tiempo, personal, etc.
- Involucra a personas de diferentes áreas y turnos: industrialización, mantenimiento, producción, logística, etc.
- Despliega el proyecto gradualmente, con objetivos realistas y alcanzables, sobre todo al principio.
- No te saltes etapas: implementa las etapas SMED en el orden establecido y registra los logros de cada una de ellas.
- Por último, piensa que el tiempo de cambio de formato siempre es mejorable: cuando termines la primera vuelta, empieza de nuevo, seguro que queda mucho por hacer.