El OEE es una métrica que mide la eficiencia operativa de los equipos. Este indicador refleja la capacidad productiva real de los equipos industriales y pone al descubierto los despilfarros del proceso (rechazos, interrupciones, averías, baja velocidad, etc.) que impiden que funcionen a pleno rendimiento.
La medición del OEE (Overall Equipment Effectiveness) se aplica a cualquier proceso productivo que tenga un estándar de trabajo definido previamente.
El OEE se expresa en porcentaje y su valor siempre se encuentra entre el 0% y el 100%, representando el 100% la situación óptima de producción: sólo se fabrican piezas buenas, a la máxima velocidad y sin paradas.
La mayoría de empresas opera con niveles de OEE por debajo del 70%, lo que supone una importante pérdida de dinero, y un gran margen para la mejora.
En el cálculo del OEE se tienen en cuenta tres variables: calidad, velocidad y disponibilidad.
- Calidad: se obtiene a partir del cálculo de piezas buenas a la primera frente al total de piezas producidas.
- Velocidad: este parámetro indica lo fabricado (bueno y malo) durante el tiempo de operación, respecto de lo que tenía que haber fabricado a tiempo de ciclo ideal.
- Disponibilidad: resulta de dividir el tiempo de operación entre el tiempo planificado de producción.
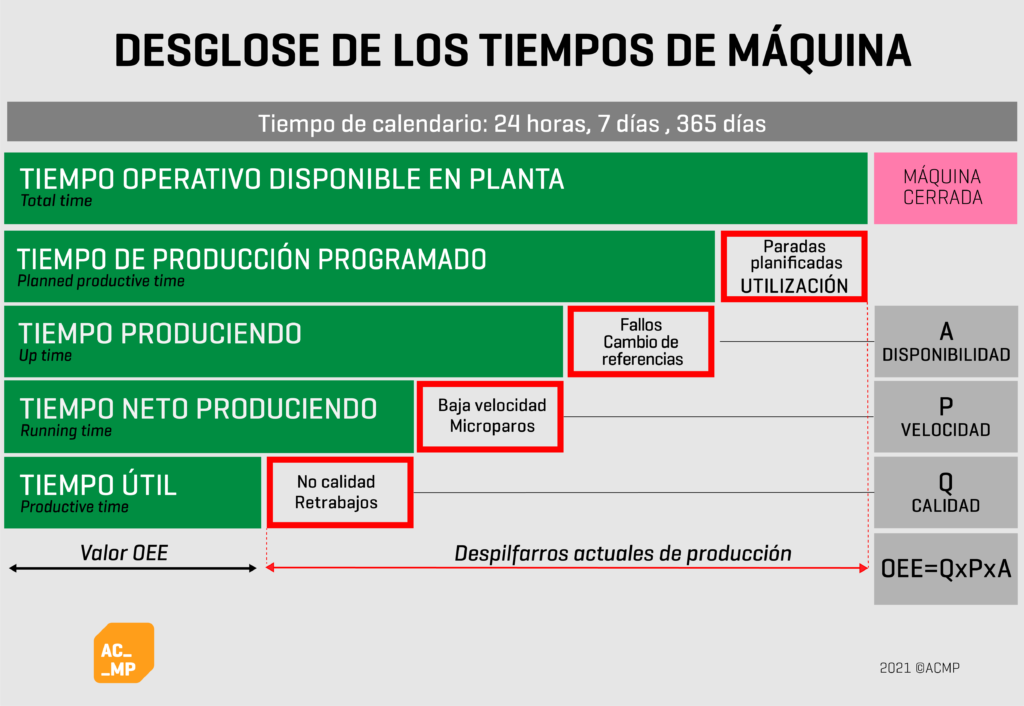
Medir, analizar, mejorar
El OEE es la mejor métrica conocida para optimizar los procesos de fabricación.
La información que proporciona permite a la empresa saber en cada momento cómo están funcionando sus equipos y líneas y dónde se producen las pérdidas para tratar de eliminarlas o reducirlas inmediatamente.
Se pueden introducir cambios con el fin de mejorar el proceso, pero sin los datos adecuados, será muy complicado acertar con las medidas.
La disminución de los despilfarros repercute positivamente en los costes de producción y mejora la calidad, lo que eleva el grado de satisfacción del cliente.
A largo plazo, el OEE supone un instrumento muy valioso para evaluar el impacto de las acciones de mejora, encauzar la estrategia y avanzar en la mejora continua.
No obstante, aunque está considerada una métrica clave para tomar decisiones dirigidas a maximizar la rentabilidad económica del proceso, todavía muchas empresas no cuentan con un sistema de medición del OEE.
Según el último estudio sobre la industria 4.0 en Navarra1, el 43% de las pymes industriales encuestadas no mide el OEE y sólo un 24% utiliza algún sistema de captura automático de datos de producción. En empresas de gran tamaño2, aunque el dato es más favorable, el 10% reconoce que no tienen procedimentada la toma del OEE y un 20% lo hace de forma manual y con pocos estándares.
Implementar un sistema de recogida y análisis del OEE
1. En el inicio del proyecto, se identifica a las personas involucradas de cada departamento, que serán buenas conocedoras del proceso. Se puede empezar en un área piloto para su despliegue posterior al resto de la fábrica.
2. Comunicar los objetivos y alcance del proyecto a todos los miembros del equipo.
3. Otro de las actuaciones es formar al equipo en los conceptos, métodos y herramientas que se van a utilizar. Es vital hacer partícipe al personal de los procedimientos y estándares para que los datos recogidos sean fiables y se eviten fallos por falta de conocimiento.
4. Definir la metodología de trabajo: establecimiento de un proceso regular de medición y revisión del OEE, datos de producción e indicadores, herramientas y sistemas.
5. Si la empresa no cuenta con uno, es prioritario implementar un sistema de gestión operativo (SGO) que permita al equipo analizar los resultados del OEE y las causas de las pérdidas en periodos cortos (turnos, día) para actuar con rapidez.
6. Elección del sistema de recogida de datos. Se puede comenzar con la recogida manual de datos, bien en hojas de Excel o mediante una herramienta digital tipo checklist. La información se colecta a pie de máquina para su posterior explotación mediante herramientas BI. Es recomendable evitar la recogida en papel para prevenir errores en las trascripciones y pérdidas de tiempo.
Con el tiempo, se puede avanzar hacia la automatización de este proceso. Un sistema automático de recogida y análisis de datos mejora y agiliza la toma de datos, proporciona métricas detalladas en tiempo real e históricos, reportes mucho más completos, así como la posibilidad de integración con otros sistemas operativos instalados en la fábrica (ERP, BBDD).
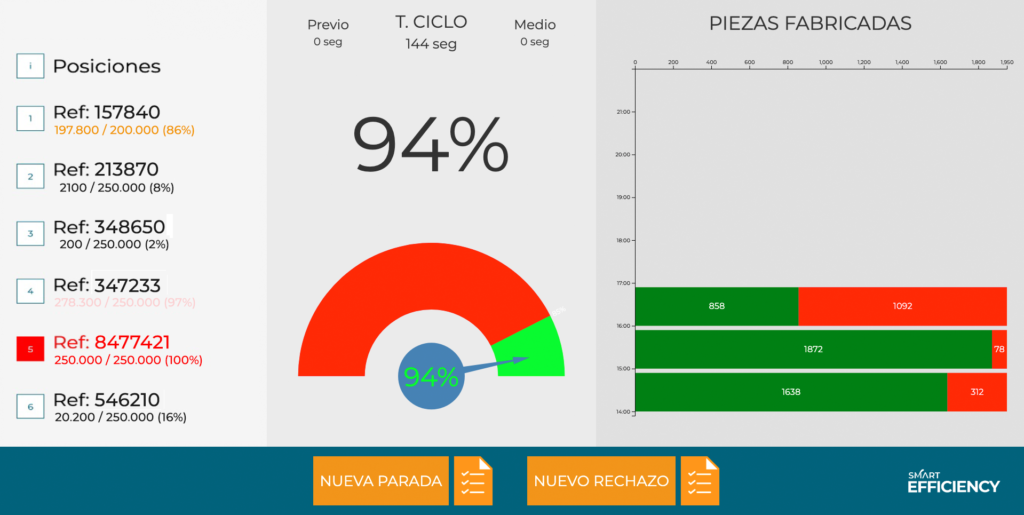
Quieres saber más sobre este servicio? Escríbenos con tus preguntas a info@acmplean.com o a través del formulario de contacto.
1. Diagnóstico de Industria 4.0 en Navarra 2020. Sobre una muestra compuesta por empresas de gran tamaño (14,14%), pymes (63,93%) y micropymes (16,23%).
2. Estudio Smart Industry 2019 España. Muestra formada por multinacionales líderes en su sector.
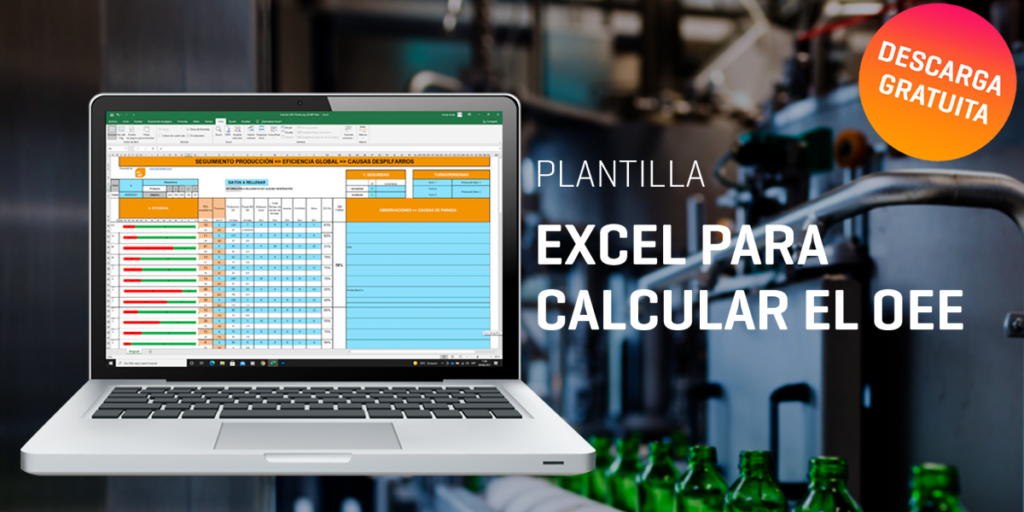
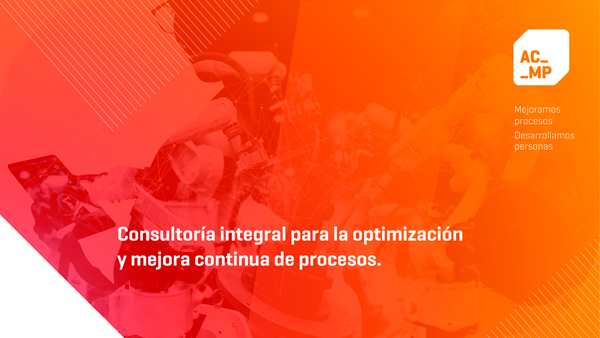
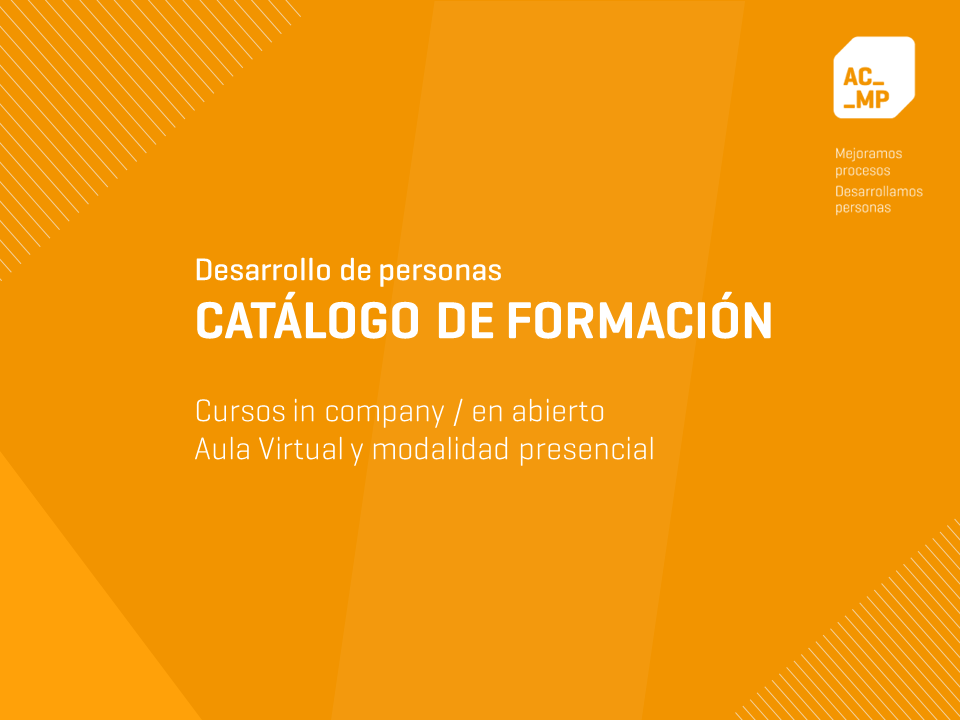
Últimas entradas
- ebook gratuito crecer sin colapsar
- ¿Reuniones improductivas? cómo convertirlas en una herramienta imprescindible para mejorar tu operativa
- ¿Tu pyme crece pero tu equipo está desbordado? Necesitas una organización sólida y elástica para dar el salto con garantías
¡Síguenos!